- Home >
- Security and Safety Insights >
- Case Study: Developing Southern Company's Lockout-Tagout Program
Case Study: Developing Southern Company's Lockout-Tagout Program
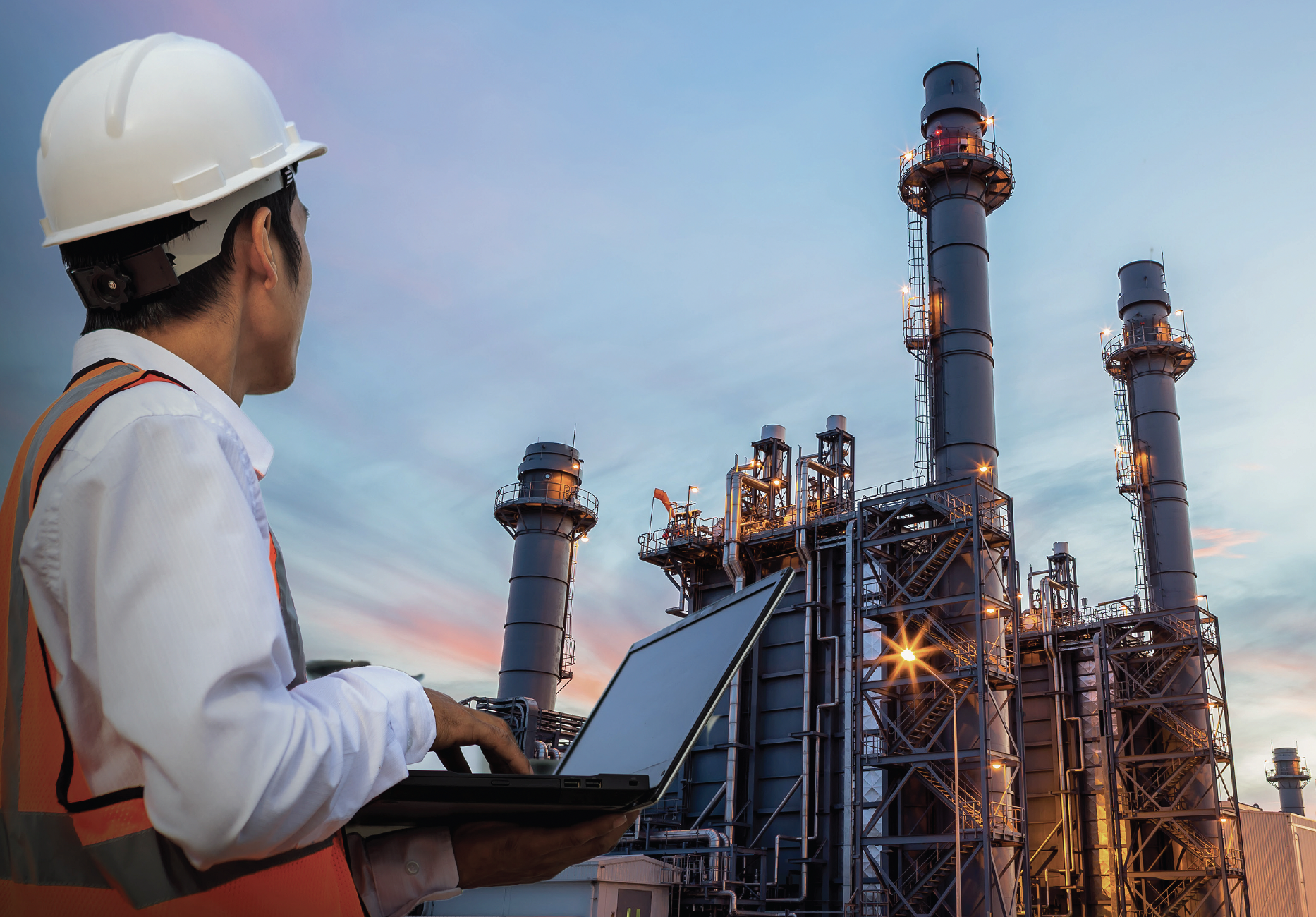
Lockout Facility Safety Case Study
Southern Company is a nationally recognized provider of energy, fiber optics and wireless communications solutions and is ranked among the top utilities in Fortune’s annual “World’s Most Admired Companies” list for electric and gas utilities.
Southern Company provides clean, reliable and affordable energy to nine million customers through its subsidiaries. Operating nearly 200,000 miles of electric transmission and distribution lines and more than 80,000 miles of natural gas pipeline, Southern Company brands are known for reliability and innovation.
As America’s premier energy company – and ranked among the top employers nationally by Forbes – Southern Company is committed to providing a safe work environment for employees and continuously implements best-in-class safety procedures to ensure OSHA compliance.
1 Southern Company Newsroom: Southern Company Named No. 14 on Forbes’ Ranking of America’s Best Employers
2 Southern Company Newsroom: Southern Company named to Fortune’s most admired list
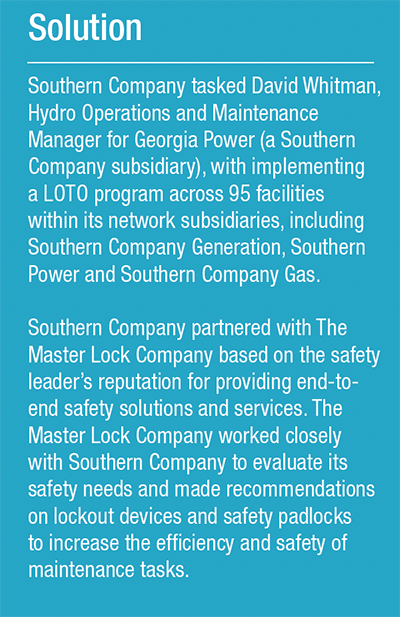
Goals & Analysis
Switching from Tagout to Lockout-Tagout Program
To improve overall employee safety across 95 of the company’s plants and facilities, Southern Company Generation made the decision to switch from a tagout-based safety program to a lockout-tagout (LOTO) program. After reaching out to colleagues in the utility industry and understanding their safety programs, Southern Company concluded it could improve overall safety by implementing a LOTO program that included lockout devices that prevent the start-up of machinery while maintenance activities are occurring.
Criteria for switching to a LOTO program included finding a partner that has 1) the ability to support large-scale operations; 2) a safety product portfolio that supports various utility maintenance tasks, including maintenance on electric, gas and power equipment; and 3) identification methods that make lockout equipment distinguishable for employees in different departments.
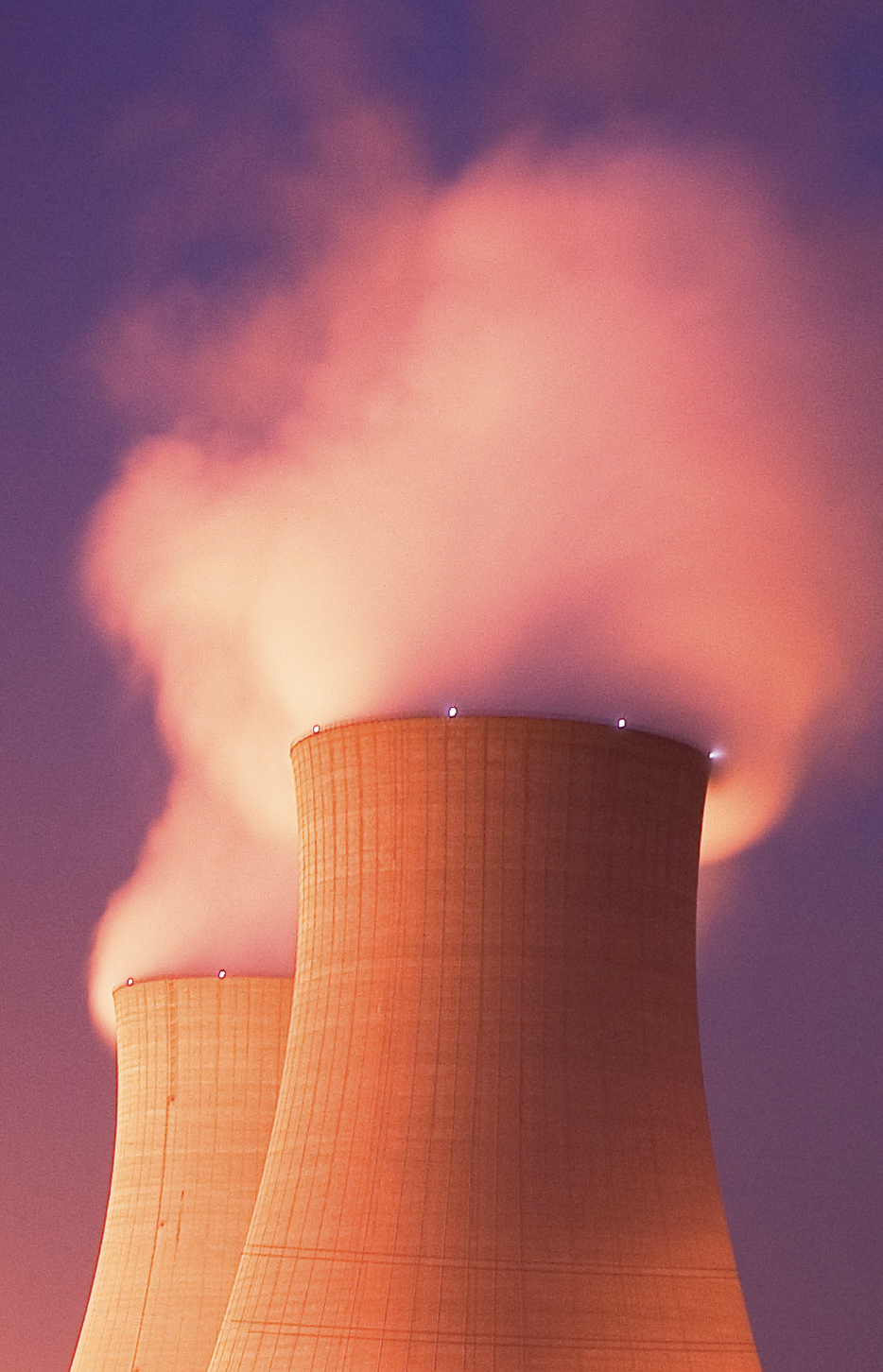
The following are solutions and procedures put in place to address Southern Company’s safety challenges:
Access to Lockout Equipment
While a tagout solution is an approved procedure under OSHA regulations for the utility industry, lockout provides an added layer of safety by providing a keyed mechanical solution that prevents unexpected start-up of machinery or equipment. By combining procedures into a LOTO program – one that involves both lockout and tagout – employees are better able to recognize when maintenance is taking place while providing workers with the peace of mind that the equipment will remain de-energized until the lockout device is removed using their key.
To implement LOTO across its generating facilities, Southern Company evaluated all areas where tagout was previously applied and determined the number of physical lockout devices needed across facilities. More than 170,000 safety products were ordered as a result, including Master Lock safety padlocks, group lock boxes and other LOTO devices, making it easier for employees to access lockout equipment and perform LOTO procedures.
Increasing Safety Efficiency
In a time-intensive industry like utilities, it was important for Southern Company to maintain efficiency when conducting LOTO procedures. And with more than 170,000 safety devices being implemented across 95 facilities, this meant finding safety solutions that 1) kept lockout devices organized and readily available, 2) were identifiable by work department or maintenance task; and 3) ensured any new padlocks ordered would not create a key duplication situation within the facility, thus maintaining the ‘one person, one lock, one key’ accepted practice.
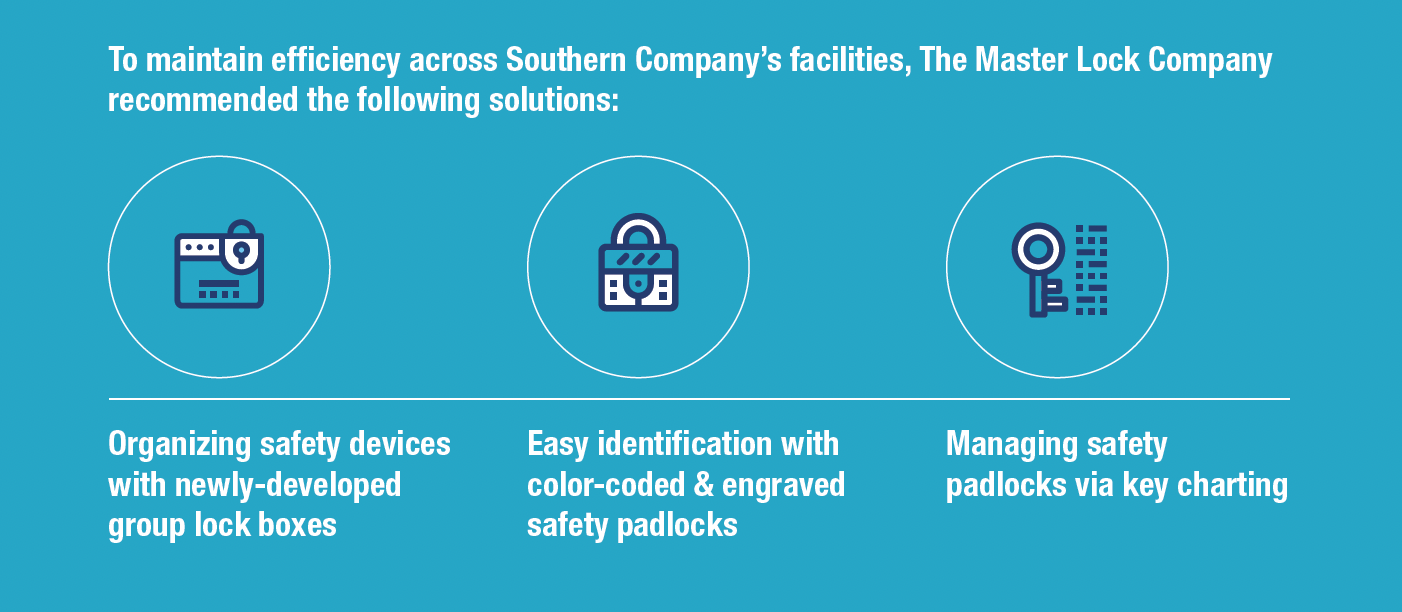
Organizing safety devices with newly-developed group lock boxes
Understanding the need to keep its thousands of safety padlocks organized and readily available for employees, Southern Company sought a solution that requires minimal floor space and made it easy for employees to identify which keys are in-use during group lockout.
To solve Southern Company’s safety challenge, The Master Lock Company developed a new group lock box that features a clear, impact-resistant window that allows workers to see keys secured inside the box during group lockout. With its stackable, portable design, Southern Company is now able to make lockout equipment readily available where work is being done without taking up floor space and can easily transport equipment to other LOTO areas when needed, increasing efficiency.
Easy identification with color-coded & engraved safety padlocks
To designate padlocks specifically to an assigned maintenance person or group, Southern Company decided to implement Master Lock’s color-coded safety padlocks. Using six different padlock colors, the safety padlocks provided Southern Company with visual recognition to the function and purpose of each padlock. For example, red safety padlocks were chosen specifically for locking out energy sources while blue padlocks were assigned to individual employees who perform LOTO across multiple facilities.
Additionally, padlocks are laser engraved to designate specific departments and facilities within Southern Company that own the locks. The laser engraving information also includes key numbers and other information that allows Southern Company to keep the locks organized and allow for easy replacement if needed.
Managing safety padlocks via key charting
Due to the sheer volume of padlocks deployed throughout Southern Company, The Master Lock Company used its key charting system to manage key codes within facilities, and in the case of personal locks, across the entire network of Southern Company facilities. The Master Lock Company’s key charting system helps to mitigate any unwanted key duplication within each facility.
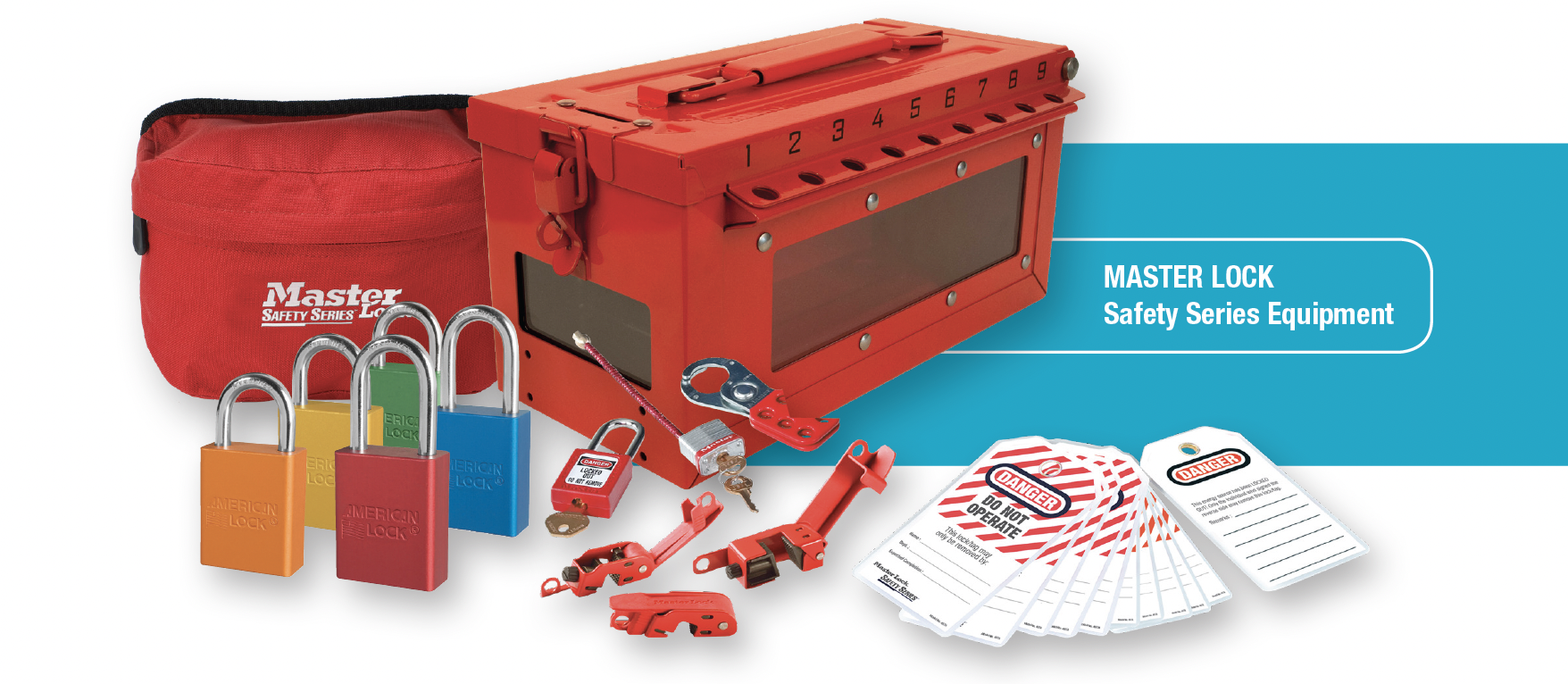
Employee Training
As part of the LOTO implementation, Southern Company conducted training for employees across its 95 facilities. The three-day training ensured each employee involved in relevant utility maintenance tasks was trained on LOTO procedures and able to perform maintenance tasks using lockout devices.
Results
After implementing LOTO procedures across its 95 facilities, Southern Company has improved employee access to lockout equipment and ultimately created a safer work environment for its employees.
Specific results include:
- Improved employee safety – Lockout devices provide an extra layer of safety when performing maintenance tasks, improving overall safety for employees.
- More uniform and consistent application of lockout – All necessary equipment is quickly and easily accessible. Employees across all facilities were trained on how to use the devices in conducting lockout procedures.
- Customer satisfaction – Southern Company rated overall satisfaction of Master Lock’s safety products and services 4.9/5 stars.
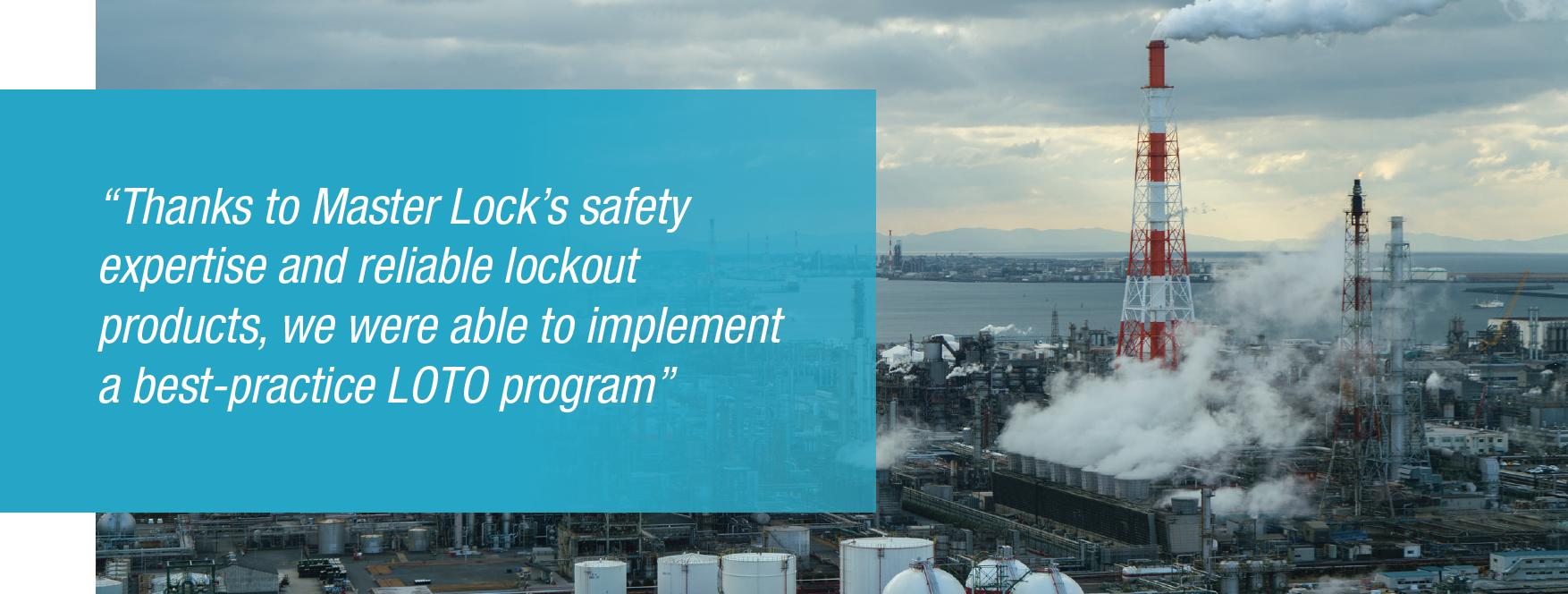
Testimonial
“It was important for Southern Company to implement a LOTO program that ensures the safety of our workers while maintaining operational efficiency and excellence. Thanks to Master Lock’s safety expertise and reliable lockout products, we were able to implement a best-practice LOTO program that improved employee access to lockout devices, maintained operational efficiency and created an even safer work environment for our employees. Master Lock has proven to be a great safety partner and I’d recommend their safety products and services to utility companies of any size looking to implement a LOTO program.”
– David Whitman, Operations and Maintenance Manager at Southern Company’s Georgia Power
Have a similar challenge? Don’t know where to start? Contact one of the Master Lock safety experts to start a conversation to see how we could help.
Visit MasterLock.com to learn more about Master Lock’s Professional Lockout Services.